

​
THE ARTIST
I'm Kate, a Birmingham-based printmaker and textile artist, working in a sustainable and environmentally conscious way.
Ink is in my blood. I spent a lot of time as a kid in my uncle’s letterpress print shop in Cheltenham, which started trading in Tivoli, Cheltenham in 1956. At 14, I officially joined the family business and began to learn the craft while also exploring my own artistic direction. My teenage years were spent working in time to the background clunk of the presses, finishing print jobs with the smell of printing ink, lead, wood and paper heavy in my nostrils. I left home – and the business - to study art at university, but my love of printmaking remained a personal passion.
After studying for an art foundation at Gloucestershire University, and then later a degree in Music Industries at Birmingham City University, I pursued a career organising music festivals; working with Kambe Events, Shambala Festival, Swingamajig Festival, and Royal Birmingham Conservatoire. My experience with high-level event work enriched my work ethic, core values, and design insight. After twelve years of putting on parties, I decided to hang up my event manager hat and don my printmaker's overalls full-time. So here I am, carving blocks, scratching plates, and inking up machines.
​
Print is back in the forefront of my life. My main love in life is creating, and then sharing those creations and the knowledge behind them. I’m an active member of British Printing Society, Stirchley Printworks, and a regular press demonstrator at The Winterbourne Press.
​
THE WORKSHOP
My workshop is my favourite room and I've spent years developing the space and the equipment it contains.
There's something romantic about hand-burnishing a single print or a small run and so I pull a lot of relief prints by hand, However, the numerous surfaces and methods I work with require the use of a variety of different printing presses – each of which has a unique character
Most of my letterpress jobs are printed on my T/P48, a post war press with an unusual design. The D-shaped inking cylinder, along with rollers, moves back and forth onto a static platen that holds the paper. I was searching for a T/P48 for some time before acquiring one though my British Printing Society connections. I enjoyed the process of lovingly restoring it to its former workhorse glory almost as much as I now enjoy printing on it.
I use my antique nipping press for printing carved lino, especially when printing onto thicker card stock or fabric. Printing with the nipping press is a manual process, but the print quality it produces is worth every heavy turn of the screw.
For drypoint work, I always use my etching press, but satisfyingly it prints everything: collagraph plates, lino, carved wood, and even lead type. I wouldn't be without it.
Finally, I have a lino/leaver press, a couple of tabletop Adana presses, and an Adana HQ press, the last of which is handy for letterpress proofs. The rest of the workshop space is taken up with type cabinets, paper cupboards, ink and sundries, hanging rollers, brayers, and silk screens, along with a 17" guillotine and a thermograph machine.

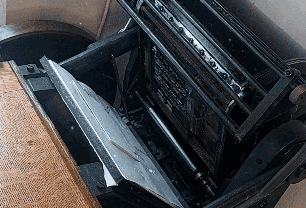
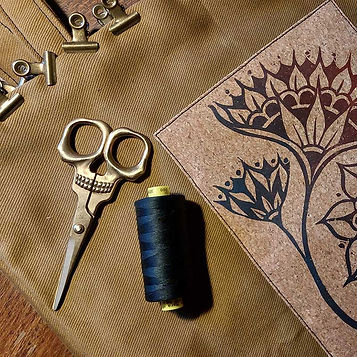
THE STITCHERY
I’m not only a printmaker, I also a textile artist and seamstress. There’s nothing more satisfying than printing textiles then handcrafting high-quality bespoke items from the fabric.
I’m a bag lover and always have been, always on the hunt for unique and environmentally friendly bags, which, it turns out, are fairly hard to find! I strive to make bags that are sturdy and reliable, practical and good-looking, long-lasting and good for the planet.
I source sustainable organic cotton and cotton canvas, some of which I dye myself using natural botanicals. I then sew everything together using strong thread made from recycled plastic bottles. The environmental impact is considered at each stage of production, from sourcing raw materials, traditional print and dying methods, and the final construction on my industrial standard Janome machine.